Maintenance of fire safety systems (S.S.I.)
Preventive maintenance of fire safety systems (SSI) is crucial for buildings open to the public (ERP), buildings for workers and high-rise buildings (IGH). This maintenance involves a complete check of all system components: central equipment as well as peripherals such as automatic smoke detectors, manual triggers (DM), evacuation diffusers, actuated safety devices (DAS)...
Why maintain your ISS?
A Fire Safety System (SSI) is a device for protecting people and property, which can comprise a Fire Detection System (SDI) and a Fire Safety System (SMSI) for the most demanding sites.
It is the responsibility of the plant manager to ensure the safety of his staff, the
sustainability of his operation and to limit the impact on the environment.
The SSI is a system waiting to be called upon, and must be operational even several years after it has been installed.
Regular maintenance visits are not only compulsory, they are also essential to confirm the plant's level of performance by carrying out periodic functional tests.
Preventive maintenance of an SSI allows :
- reduce the probability of plant failure,
- minimize corrective maintenance operations,
- make any necessary repairs and/or improvements,
- to ensure long-term operation and guarantee your initial investment.
- to guarantee optimum safety.
You need a personalized diagnosis
Our teams are at your disposal to answer any questions you may have.
What maintenance operations need to be carried out on your SSI?
Two maintenance visits per year are recommended (or even mandatory in some cases), and include various operations:
- Examination of operating documents (operating and maintenance manual, safety register, APSAD declaration or installation technical file).
- Visual inspection of installation (SSI control lights, equipment integrity, suitability of system for building operation, etc.).
- Functional testing of scenarios and system components (DAS, AES, automatic detectors, manual releases, etc.)
Reduce
Discover
Why choose Eurofeu?
Our teams are trained and qualified to carry out the necessary checks and maintenance, and to bring your fire safety systems up to standard, on all types of fire safety systems (fire safety systems categories A to E) and on all types of alarm equipment (EA types 1, 2a, 2b, 3 and 4). Our multi-brand, multi-trade expertise means we can advise you effectively on optimizing your fire safety.
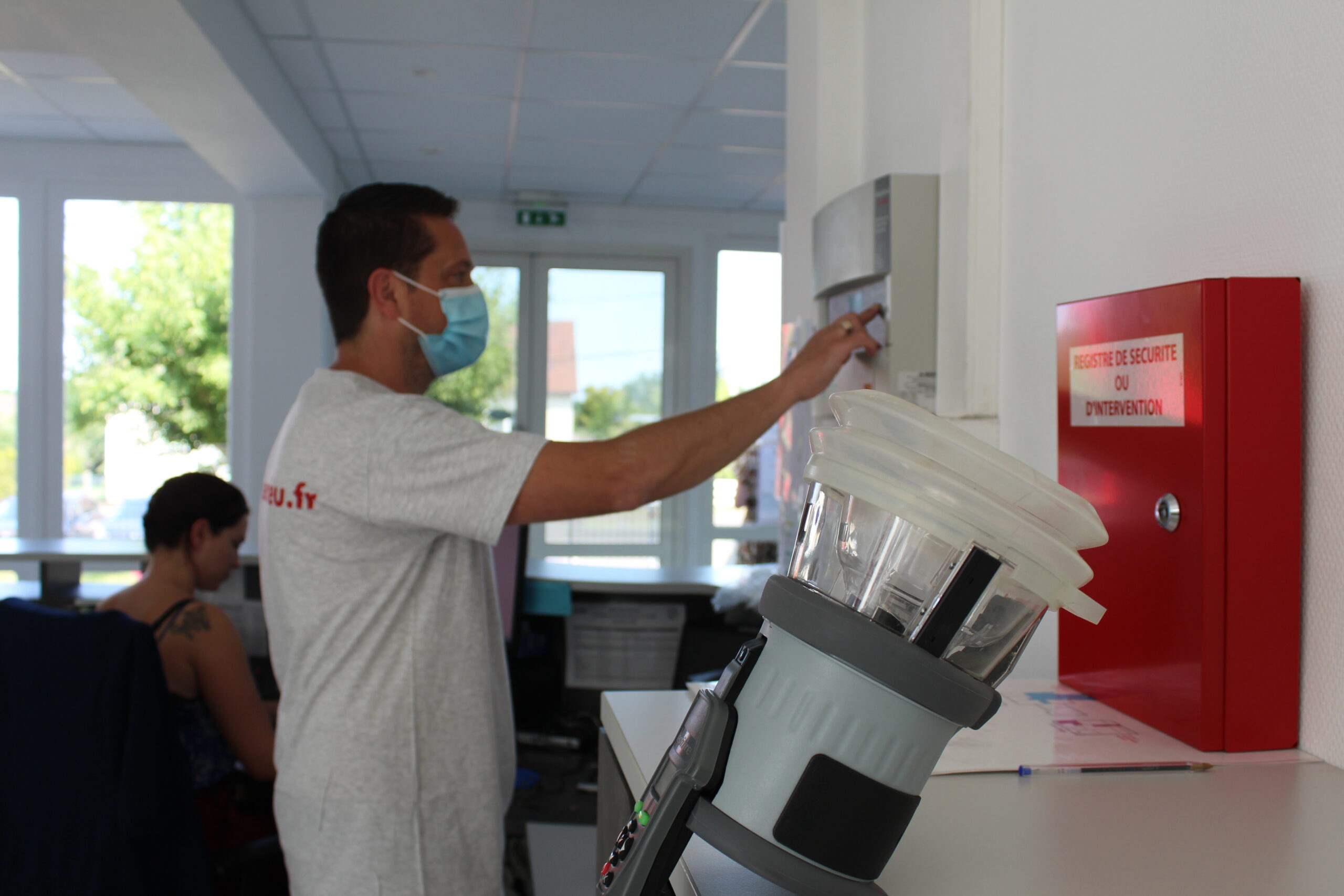
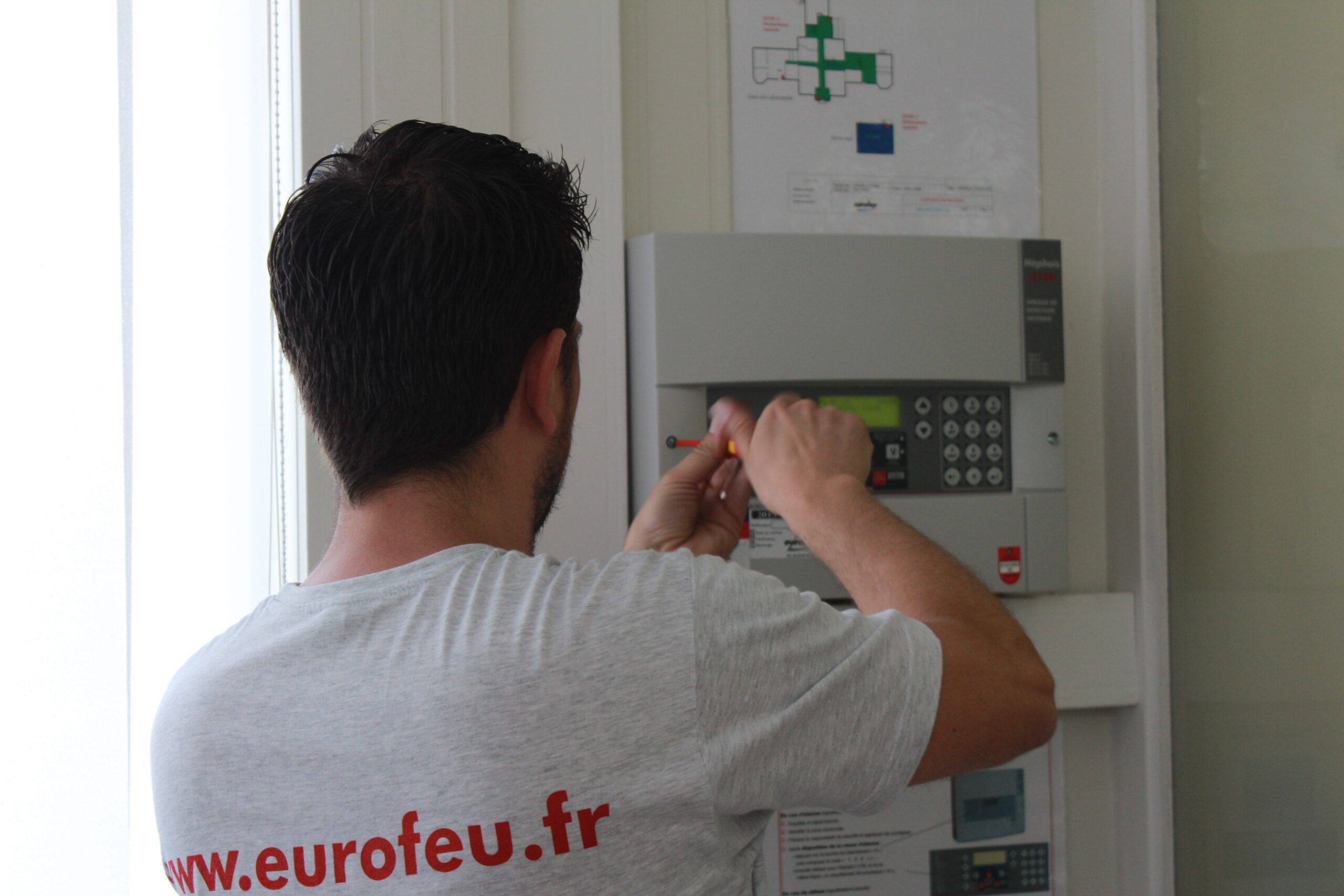
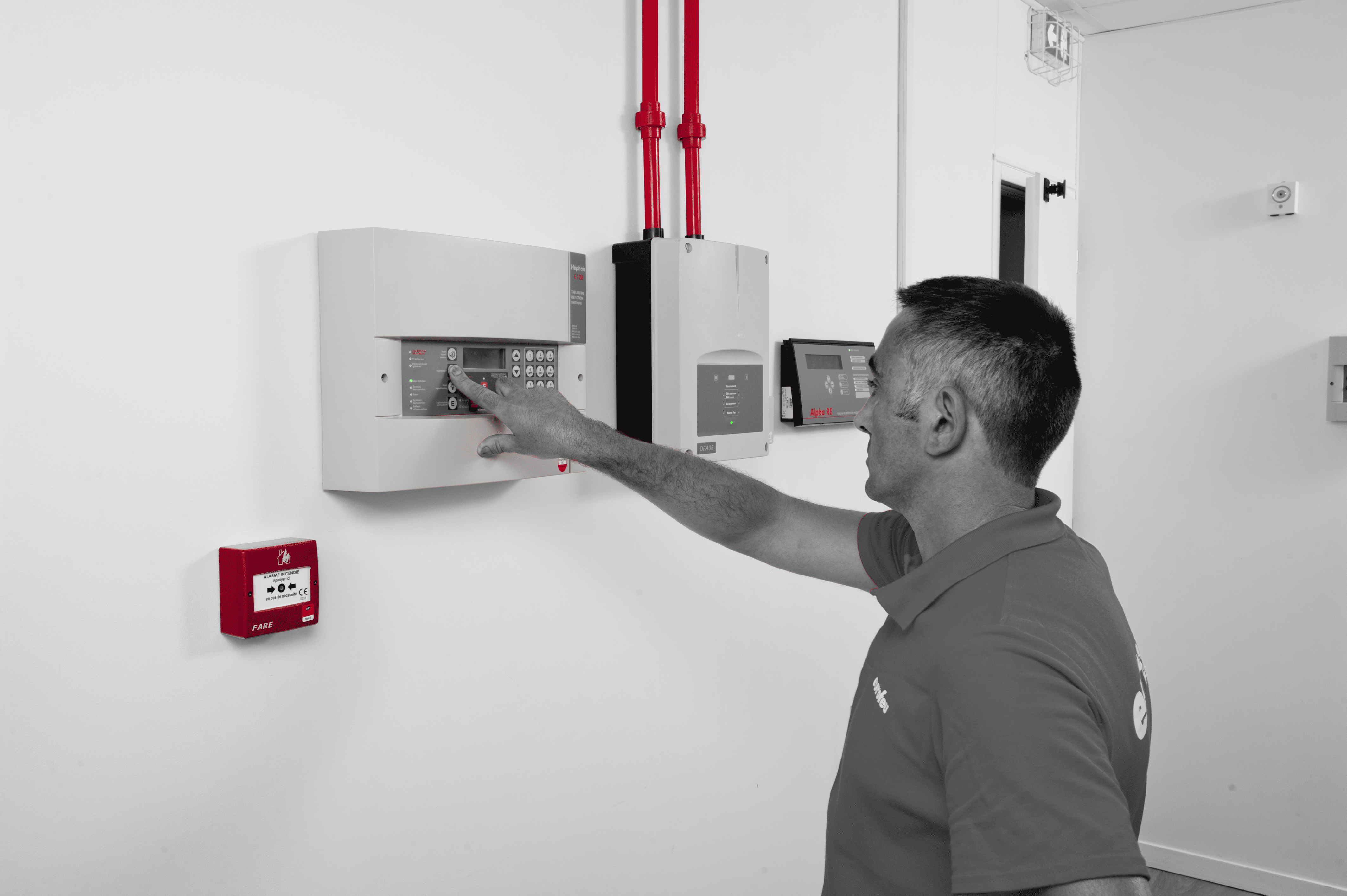