What is the importance of PPE?
Personal Protective Equipment, better known by its acronym PPE, plays a crucial role in the professional world. It is a device put in place to guarantee the safety of workers, protecting them against various risks associated with their activity. The use of PPE, from gloves to goggles, minimizes the risk of accidents or injury in the workplace. This is a regulatory standard in France, which underlines the importance of health and safety in the workplace.
Understanding the meaning of PPE
The role of Personal Protective Equipment
Personal protective equipment (PPE) plays a crucial role in accident prevention in the workplace. They are used to protect workers against a multitude of occupational hazards that could affect their health or safety. This equipment includes a number of essential elements:
- Head impact helmets
- Protective goggles against metal splashes
- Gloves to avoid superficial lesions
- Safety shoes to protect feet from falling objects
It is the employer's responsibility to ensure that PPE is in good condition and suitable for specific tasks. Regular assessment is necessary to verify their effectiveness. For example, a helmet should be checked to ensure that it has not been damaged by a previous impact. The well-being of workers depends on the correct use of such equipment, and proper training is often required to ensure its optimal use.
Definition of PPE
Personal Protective Equipment, or PPE, is essential for worker safety. They are used to protect against various hazards present in the working environment. PPE includes a variety of items:
- Helmets that protect the head from impacts
- Gloves that prevent cuts and burns
- Masks that filter out dangerous particles
This equipment must be adapted to the specific risks of each workstation. It complements the collective protection measures already in place. Their effectiveness depends on correct use and compliance with current standards. Regular monitoring ensures that the equipment is in optimum working order. In some sectors, such as construction or the chemical industry, wearing PPE is not only advisable but often compulsory, ensuring adequate protection against potential hazards.
What does E.P.I. stand for?
E.P.I. stands for Personal Protective Equipment. This equipment is essential to ensure workers' safety in the face of the many hazards present in the workplace. It includes various elements designed to protect against specific risks.
Common PPE includes :
- Helmets to protect your head
- Safety eyewear
- Hand gloves
- Earplugs for noise exposure
PPE is governed by strict standards to guarantee its effectiveness. Their choice must be adapted to the tasks to be performed and the risks identified. For example, in the construction sector, a helmet is essential to prevent injuries caused by falling objects. In short, PPE plays a crucial role in preventing occupational accidents.
PPE categories
List of PPE types
There are several types of Personal Protective Equipment (PPE) to meet the needs of different occupational hazards. The main categories are as follows:
- Head protection: helmets, caps, capes.
- Eye and face protection: goggles, over-glasses, masks.
- Hearing protection: earplugs, earmuffs.
- Respiratory protection: masks with filter cartridges, respirators.
- Hand protection: gloves suitable for various chemical or mechanical hazards.
- Foot protection: safety shoes, boots.
- Body protection: high-visibility clothing, chemical suits.
- Fall protection: harnesses, lanyards, fall arresters.
Each type of PPE is designed for specific protection and must be selected according to the risks identified in the workplace. This equipment is essential to ensure the safety of workers in a variety of working environments.
PPE specific to each sector of activity
Personal Protective Equipment (PPE) varies from sector to sector to meet the specific hazards of each working environment. In the construction industry, workers often need helmets, resistant gloves and safety shoes to prevent injury from falling objects.
In the chemical sector, specific respirators and coveralls are essential to protect against the inhalation of hazardous substances.
For healthcare workers, high-filtration gloves and masks are used to limit exposure to pathogens.
Each sector therefore requires appropriate PPE to guarantee employee safety in the face of identified risks.
The choice of PPE must take into account current standards and the specific needs of workers to ensure effective and compliant protection.
PPE: a standard or an obligation?
Personal Protective Equipment (PPE) is not just a standard, but a legal obligation in France. Under the French Labor Code, employers must ensure the safety of their employees by providing PPE appropriate to the risks identified.
Obligations include :
- Free supply of essential equipment
- Training and informing employees on the correct use of PPE
- Regular verification of equipment conformity
Employers must also ensure that PPE is adapted to the specific tasks of each worker and complies with current standards. For example, in the chemical sector, respiratory masks adapted to the substances handled are essential. Compliance with these obligations not only helps to protect workers' health, but also avoids legal penalties for the company.
The importance of wearing PPE in the workplace
Why do I need to wear PPE?
Wearing Personal Protective Equipment (PPE) is a necessity to minimize occupational hazards. This equipment acts as a barrier between the worker and potential workplace hazards.
PPE helps prevent serious injury and reduce exposure to harmful substances. For example, workers in the chemical sector use breathing masks to prevent inhalation of hazardous products.
There are many advantages to wearing PPE:
- Protection against accidents and injuries
- Reducing absences due to occupational illness
- Increased productivity thanks to a greater sense of security
It is essential that PPE is correctly adapted to the specific tasks of each employee to maximize its effectiveness. In addition, proper training in their use is essential to guarantee optimum protection.
PPE: a guarantee of safety in the workplace
Personal protective equipment (PPE) is a fundamental element in ensuring safety in the workplace. They considerably reduce the risk of accidents and occupational illness by creating a protective barrier between the worker and potential hazards.
PPE must be carefully selected to suit the specific risks associated with each workstation. Their effectiveness depends on their correct use, and on the match between the type of equipment and the hazard identified. For example, in a noisy environment, adequate hearing protection is essential to prevent hearing loss.
Employers are responsible for training their employees in the proper use of PPE. This training includes the correct fitting of equipment and an understanding of the risks it covers. Ongoing awareness of the importance of PPE reinforces the company's safety culture.
The consequences of not wearing PPE
The absence of Personal Protective Equipment (PPE) exposes workers to considerable risks, which can lead to serious injury or occupational illness. Without PPE, companies expose themselves to serious consequences, including legal action, as their civil and criminal liability can be called into question in the event of an accident.
The consequences for employees include an increased risk of workplace accidents. For example, a helmetless worker on a building site risks injury from falling objects.
For the company, the repercussions go beyond the legal framework:
- Loss of reputation: An accident due to lack of PPE can damage the company's credibility.
- Financial impact: Accidents entail costs in terms of time off work and compensation.
It is therefore vital to integrate PPE into the company's safety culture to avoid these negative impacts.
Legal requirements for PPE in France
In France, legal obligations concerning Personal Protective Equipment (PPE) are strictly governed by the Labor Code. Employers are required to provide PPE adapted to the risks identified in the workplace. This equipment must comply with current standards and be appropriate to the specific tasks of each employee.
Companies must also ensure that PPE is used correctly. This means training workers in their use. This training must be regular to keep employees' skills up to date.
It is crucial that the employer implements regular monitoring to ensure the condition and compliance of PPE. Obligations also include maintenance and replacement of defective equipment. Penalties for non-compliance can include fines and increased liability in the event of an accident.
Current PPE regulations and standards
Personal protective equipment (PPE) is subject to strict regulations to ensure user safety. In France, PPE must comply with European or international standards, such as ISO or EN, to guarantee its quality and effectiveness.
Before being marketed, they undergo rigorous testing to verify their compliance with performance requirements. These tests include specific test methods for each type of equipment.
Category III PPE, for example, requires continuous production monitoring to ensure that it protects against serious hazards. All PPE must be clearly marked, including manufacturer identification and compliance with standards.
Companies must also provide detailed instructions, including advice on the use and maintenance of PPE, to ensure optimum protection.
The company and its responsibility with regard to PPE
Employer's role in supplying PPE
Employers have several key responsibilities when it comes to supplying Personal Protective Equipment (PPE) to their employees. They must ensure that PPE is appropriate for the risks identified, and complies with current safety standards. In addition, this equipment must be provided free of charge to employees.
It is also crucial that the employer implements regular monitoring to ensure that PPE is in good condition. This includes maintenance, repair and replacement of defective equipment. The employer must also inform and train employees on the correct use of PPE.
Employees need to understand not only how to use the equipment, but also the risks it helps to prevent. To illustrate, an employee working at height must be trained in the use of a safety harness to minimize the risk of falling. The employer's commitment to these steps reinforces workplace safety.
The importance of PPE training in the workplace
Personal Protective Equipment (PPE) training in the workplace is essential to ensure the correct and effective use of these devices. It enables employees to understand how to fit and wear PPE, thus maximizing their protection. Well-structured training often includes practical demonstrations, helping to reinforce workers' skills.
Key elements of this training include:
- Identifying the specific risks associated with each workstation
- Proper use of PPE in every situation
- Regular maintenance and inspection of equipment
A case in point: an employee working in a noisy environment needs to know how to adjust his or her hearing protection correctly to avoid hearing loss. An appropriate training program ensures that employees are informed and competent, contributing to a robust safety culture within the company.
PPE inspection and renewal: a regulatory obligation
Personal protective equipment (PPE) requires regular checks to guarantee its effectiveness and safety. Depending on the PPE category, monitoring may vary. Category III PPE, for example, must undergo strict controls by external bodies to ensure compliance.
Companies must ensure that this equipment is inspected periodically. This includes:
- Technical checks: to detect any potential defects.
- Renewal according to wear: to maintain performance.
Careful monitoring can minimize the risk of failure. For example, safety harnesses used at height need to be checked frequently by an expert to prevent accidents. This is crucial for worker protection, and complies with current legal requirements. Employers thus have a responsibility to ensure the availability of safe, high-performance PPE for their employees.
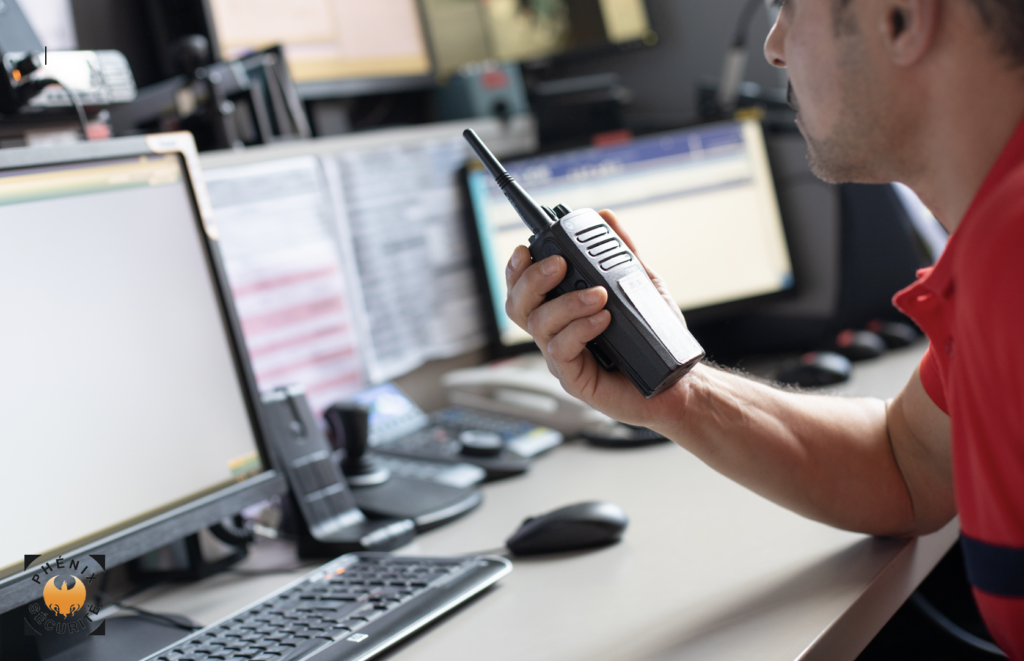